设备综合效率(OEE)是衡量生产设备实际效能的核心工具,本文将深入解析其计算逻辑,并提供实用优化建议。
一、OEE的核心公式与三大维度
设备综合效率(OEE)的计算公式为:
OEE = 时间开动率 × 性能开动率 × 合格品率
这一公式通过三个维度量化设备效率损失,帮助企业精准定位问题。
1. 时间开动率:设备的时间利用效率
时间开动率衡量设备在计划运行时间内实际工作的时间占比,计算公式为:
时间开动率 = 开动时间 / 负荷时间 × 100%
负荷时间:日历工作时间扣除计划停机(如保养、早会)和非设备因素停机(如停水停电)后的剩余时间。
开动时间:负荷时间进一步扣除设备故障、换模等非计划停机后的净工作时间。
示例:某设备计划运行8小时(480分钟),其中计划停机50分钟,非设备因素停机20分钟,故障停机70分钟。则:
负荷时间 = 480
50 -20 = 410分钟
开动时间 = 410 -70 = 340分钟
时间开动率 = 340 / 410 ×100% ≈82.9%
实用建议:
区分计划停机与非设备因素停机,避免混淆统计口径。
通过物联网技术实时监控停机原因,减少人为记录误差。
2. 性能开动率:设备的速度与稳定性
性能开动率反映设备实际生产速度与理论最大速度的差距,计算公式为:
性能开动率 = (实际产量 × 理论节拍时间) / 开动时间 × 100%
理论节拍时间:设备铭牌标注的理想生产周期(如每件产品耗时8秒)。
实际产量:开动时间内的总产量,包含不良品。
示例:某设备理论节拍时间为0.5分钟/件,开动时间370分钟内生产473件产品(含不良品),则:
性能开动率 = (473 ×0.5) / 370 ×100% ≈63.9%
实用建议:
定期校准理论节拍时间,避免因设备老化导致数据失真。
通过传感器监测设备空转、微停机(如)等隐性损失。
3. 合格品率:质量损失的直接反映
合格品率衡量设备产出中良品的比例,计算公式为:
合格品率 = 合格品数量 / 总产量 × 100%
注意:仅统计一次通过的合格品,返修品和报废品不计入。
示例:某批次生产500件产品,其中20件返修、15件报废,则:
合格品率 = (500-20-15) /500 ×100% =93%
实用建议:
建立自动化的质量检测系统,减少人工统计误差。
分析不良品与工艺参数(如温度、压力)的关联性,优化生产条件。
二、OEE计算的常见误区与修正
误区1:混淆计划停机与非设备因素停机
部分企业将“换模”“等料”等可优化停机归为计划停机,导致OEE虚高。
修正方法:
计划停机仅包含不可控的例行维护(如加油、清洁)。
可优化停机(如换模、参数调整)应计入非计划停机。
误区2:忽略非设备因素停机
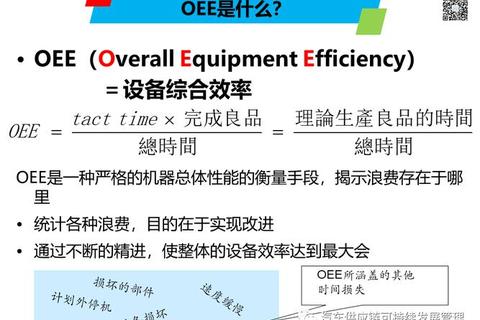
传统OEE公式未剔除停水停电等外部因素,导致数据可比性差。
修正方法:
引入设备完全有效生产率(TEEP),将非设备停机单独统计,公式为:
TEEP = 设备利用率 × OEE
其中,设备利用率 = (日历时间
计划停机
非设备停机) / 日历时间。
三、提升OEE的五大策略
1. 数据驱动的设备监控
部署传感器采集设备运行状态(如振动、温度),构建数字孪生模型。
建立停机原因分类标准,避免数据混乱。
2. 预防性维护与快速响应
制定定期保养计划,减少突发故障。
通过AI预测设备寿命,提前更换易损件(如轴承)。
3. 优化生产节奏与换模流程
采用SMED(快速换模)技术,将换模时间缩短30%以上。
平衡生产线节拍,避免上游缺料或下游堵塞。
4. 员工培训与标准化操作
定期开展设备操作培训,减少人为失误导致的停机。
编制可视化操作手册,规范日常点检流程。
5. 质量闭环管理
实时监测工艺参数(如pH值、真空度),减少批量性不良。
建立不良品根因分析机制,避免重复问题。
四、案例解析:OEE从36%到71%的改善路径
某工厂设备初始OEE仅为36%,通过以下措施提升至71%:
1. 时间开动率优化(从84%提升至92%)
将换模时间从70分钟压缩至30分钟。
建立备件库存预警系统,减少待料停机。
2. 性能开动率优化(从44%提升至85%)
校准理论节拍时间,修正设备空转参数。
通过IoT监测微停机,优化进料速度。
3. 合格品率优化(从98%提升至99.5%)
识别清洗工序pH值波动对良率的影响,调整工艺窗口。
引入自动分拣设备,减少人工漏检。
五、OEE不是终点,而是持续改善的起点
OEE的核心价值在于揭示设备效率的“冰山之下”的损失(如空转、微停机)。企业需结合TEEP、MTTR(平均修复时间)等指标,构建多维分析体系。最终目标是通过数据透明化,实现从“救火式维修”到“预测性管理”的转型。